Daily Maintenance is Essential to Extend the Service Life of Your RO Membranes
The RO membrane is powerful yet fragile. It is resistant to high pressure and chemicals, and efficiently filters, regarded as a nemesis of wastewater. However, its performance and lifespan can also be affected by factors such as raw water quality, pretreatment effectiveness, and operating conditions. Proper maintenance helps extend the lifespan of the RO membrane.
Before Use
First, preserve unused membrane elements properly. Depending on the different characteristics and requirements of manufacturing, storage, transportation, and application, membrane elements are divided into dry and wet ones. Dry membrane elements are easier to transport and install, thus with a longer shelf life than wet ones. Dry and wet membrane elements are preserved with different methods.
After Equipment Test
After 2-6 hours of system trial operation, the RO membrane can be maintained by soaking it in a 1% sodium bisulfite solution according to the preservation method of the wet membrane element.
After 15-24 hours of trial operation, a 2% formaldehyde solution can be used for maintenance. During maintenance, the air should be expelled from the equipment pipelines as much as possible, avoiding any leaks. All inlet and outlet valves should also remain closed.
During System Operation
Regular inspection for stable operation
On one hand, inspect the appearance and connections of the membrane elements. Specifically, check whether there are cracks, and damage on the membrane elements, and whether membrane elements are connected tightly to prevent leaks. On the other hand, monitor the operating parameters of the RO membrane, such as pressure, flow rate, and pressure difference, to detect anomalies and make early adjustments.
Strengthen management of the pretreatment system
Monitor and control the pH value, temperature, turbidity, and residual chlorine content of the feedwater, ensuring that substances that could pollute the membrane can be removed by pretreatment, feedwater requirements of the membrane elements are met and the membrane's burden is lightened. The scale inhibitors should be reasonably utilized to prevent calcium and magnesium ions from crystallizing on the membrane surface and forming scale layers. The content of scale inhibitors in the feedwater is generally controlled at 3-6 ppm.
Timely clean to slow down membrane pollution
Suspended solids, colloids, organics, microorganisms, and salts precipitated after concentration in the feedwater can all pollute the membrane elements, causing a decline in the performance of the membrane system. After the standardized calculation of the operating data using standardized software is conducted, chemical cleaning should be performed promptly in any of the following cases:
● The water production of the system decreases by more than 15% from the initial value
● Salt passage rate increases by more than 10% from the initial value
● Pressure difference between feedwater and concentrated water increases by more than 15% from the initial value
During chemical cleaning, it is necessary to select the appropriate cleaning agent based on the type of membrane fouling, control the concentration of the cleaning agent, and conduct periodic cleaning at the appropriate temperature and time, ensuring the cleaning effect and preventing damage to the membrane.
+86 10-83619831 | 2 | 3 | 6
Address: 1518 Liyang Avenue, Guiyang National High-tech Industrial Development Zone, Guiyang City, Guizhou Province
Marketing Center: 16th Floor, Block G, Yingkun Century, East Road, Automobile Museum, Fengtai District, Beijing
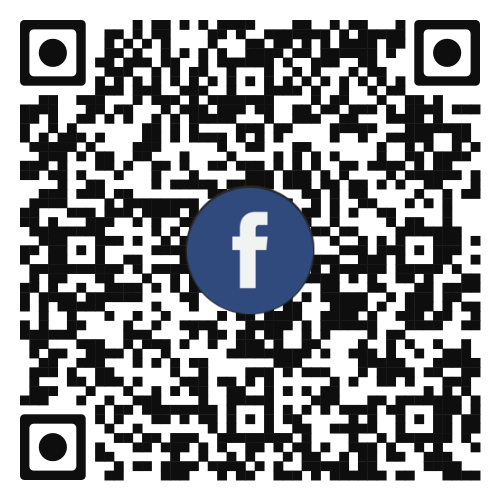
COOKIES
Our website uses cookies and similar technologies to personalize the advertising shown to you and to help you get the best experience on our website. For more information, see our Privacy & Cookie Policy
COOKIES
Our website uses cookies and similar technologies to personalize the advertising shown to you and to help you get the best experience on our website. For more information, see our Privacy & Cookie Policy
These cookies are necessary for basic functions such as payment. Standard cookies cannot be turned off and do not store any of your information.
These cookies collect information, such as how many people are using our site or which pages are popular, to help us improve the customer experience. Turning these cookies off will mean we can't collect information to improve your experience.
These cookies enable the website to provide enhanced functionality and personalization. They may be set by us or by third-party providers whose services we have added to our pages. If you do not allow these cookies, some or all of these services may not function properly.
These cookies help us understand what you are interested in so that we can show you relevant advertising on other websites. Turning these cookies off will mean we are unable to show you any personalized advertising.